The Navy estimates that 3D printing may have saved it $400,000 and allowed them to avoid a year-long wait for crucial repairs, representing a pivotal development that could lower repair costs and reduce downtime in the $31.2 billion ship building and repair industry.
Per an article published on Breaking Defense on Thursday, the crew of assault ship Bataan used a 3D printer on the ship to create a replacement of a missing air compressor within just five days while at sea, a process that the Navy says could have otherwise taken a year.
Attributable in part to authorization which the Naval Sea Systems Command signed in May, ship crews can now 3D print components considered “low criticality”, meaning they pose no harm to those on board if they fail, according to the Breaking Defense article. As of 2022, the US Navy operated 301 ships in total. This development has the potential to substantially cut fleet maintenance costs and minimize interruptions.
Approvals of 3D printing for military use have taken years. Huntington Ingalls Industries (HII), the largest military shipbuilding company in the United States, secured NAVSEA approval to methodically incorporate additive manufacturing into naval vessels. Stakeholders believe that this gradual assimilation signifies a broader future adoption of 3D printing across the industry.
The protracted approval process has been due to heightened risks, including:
- The need for standardization of the processes and procedures to ensure quality
- Doubts over the material’s structural integrity
- Questions regarding the expertise of operators
- Cybersecurity issues, including concerns about the confidentiality of blueprints
- Regulatory hurdles
- Fears of job losses as a result of additive manufacturing alternatives
Labor Concerns

While additive manufacturing has witnessed rising adoption, both within and outside the U.S. Navy, establishing significant labor trends from available data might be premature. The principal anxiety regarding 3D printing, as with wider automation fears, pivots on job loss. However, existing data showcases a rise in both gross output and total employment within the industry since 2016 and 2020, respectively, according to the U.S. Bureau of Economic Analysis (BEA) and U.S. Bureau of Labor Statistics.

A primary apprehension with 3D printing, mirroring broader automation worries, is job loss. Yet current data shows gross output as well as total employment from the industry have both been increasing since 2016 and 2020 respectively, according to data from the U.S. Bureau of Economic Analysis (BEA) and U.S. Bureau of Labor Statistics.
Back in 2022, Verisk posted about the concerns which the National Institute for Occupational Safety and Health (NIOSH) had over workplace exposure to ultrafine particles (UFP) from the use of 3D printers.
As the shipbuilding and repair industry adopts 3D printing, any impact on the industry and on the labor landscape will be most profoundly felt in the top US ports.
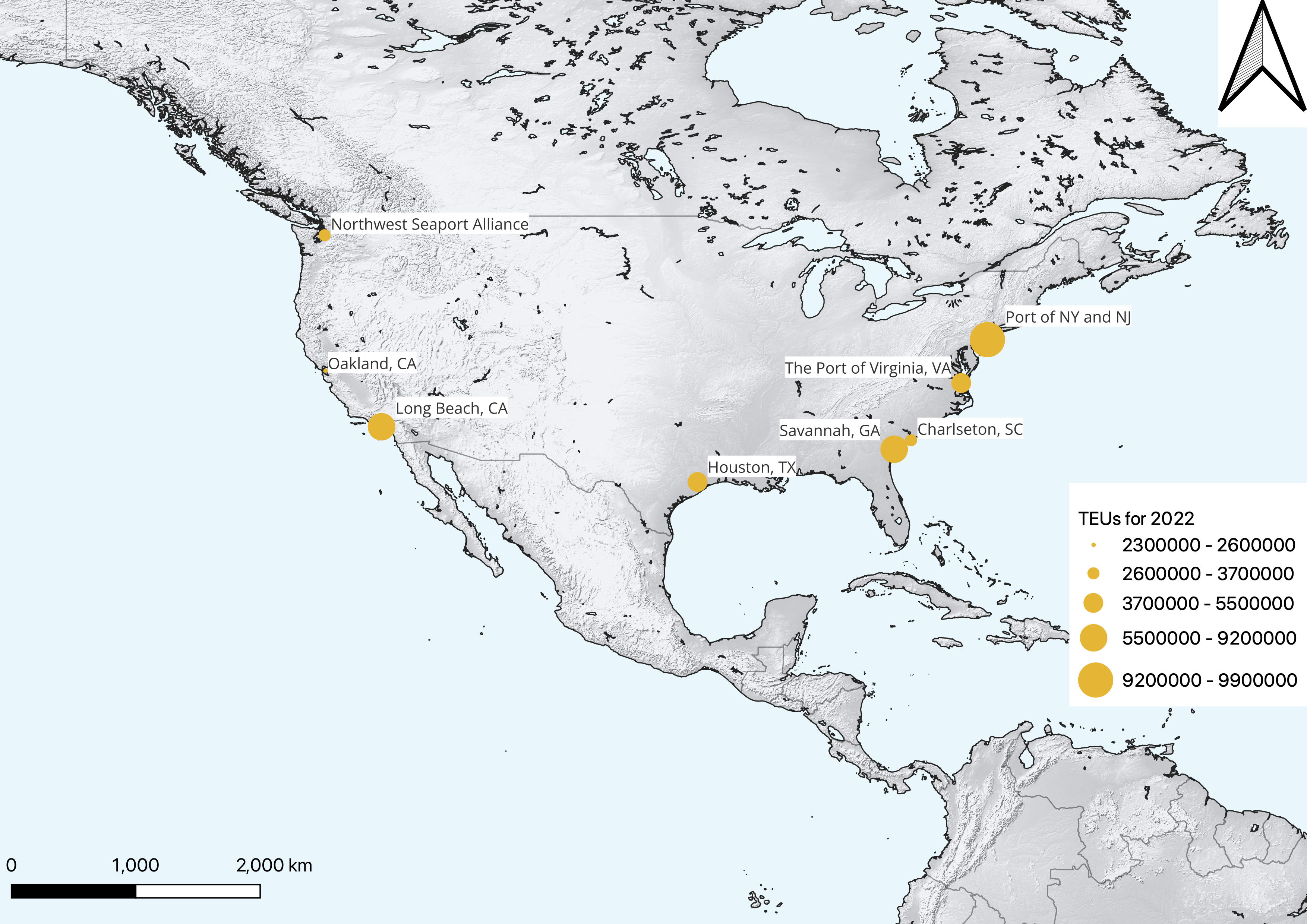